Un premier cycle de recyclage complété pour les pièces de pompe
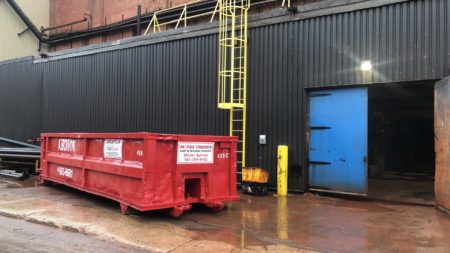
Toutes les équipes sont appelées à contribuer à la récupération des pièces de pompes, le tri des matériaux étant déterminant pour consolider le projet.
Dans un contexte où l’approvisionnement est un enjeu important et où la qualité des pièces a un impact direct sur la durée de vie des produits, récupérer les pièces de pompes remplacées représentait une belle opportunité qui n’aurait pu être possible sans l’implication des équipes.
De nombreuses pompes sont nécessaires aux opérations de l’Usine Vaudreuil. Les pièces qui composent les pompes sont fabriquées à partir de fonte à haute teneur en chrome. « Seulement pour les usines Hydrate Est et Ouest, nous faisons usage d’environ 560 pompes. Toutes ces pièces en viennent à s’user ou à se briser. Nous devons donc les remplacer régulièrement », explique Marc Tremblay, ingénieur d’entretien.
L’initiative a débuté en 2019, alors qu’un grand bac a été installé à l’extérieur de l’usine Hydrate Est afin de recueillir les pièces de métal. En développant un partenariat avec Métallurgie Castech, une fonderie de Thetford Mines qui produit la majorité des pièces de pompes, l’usine est parvenue à amasser 39 000 livres de métal en seulement 5 mois pour son premier chargement, puis 50 000 livres lors de son second. Lorsque l’usine Hydrate Ouest prendra elle aussi part au projet dans les prochains mois, on estime que la quantité de métal recyclé pourrait ainsi doubler.
« Les pièces récupérées sont acheminées au fournisseur pour ensuite être recoulées. Le métal recyclé est la matière première qui en résulte. C’est une manière de faire qui est avantageuse puisque ça nous permet de conserver la qualité initiale et de subir de façon moins drastique la hausse des coûts actuels de l’acier », poursuit M. Tremblay.
Procéder à la récupération des pièces de pompes comporte néanmoins plusieurs défis dans la pratique. Le succès d’un tel projet repose en grande partie sur la collaboration des équipes de travail sur le terrain.
« Métallurgie Castech fournit le bac. Une fois rempli, ils viennent le chercher et le crédit est appliqué. Il n’y a pas de frais inhérent à la location du bac ou à son transport. Avec l’expérience, nous en sommes venus à améliorer nos façons de faire et à revoir l’emplacement du bac qui est maintenant ceinturé d’une clôture et identifié au nom de la fonderie », précise Michaël Allard, technicien d’entretien à l’usine Hydrate Est.
Mobilisation et sensibilisation : la clé du succès
« Nous récupérons déjà beaucoup de matière : du bois, de l’acier, du plastique, mais il fallait faire comprendre à tous les employés que dans ce cas-ci, ce qu’on voulait recycler, c’était uniquement les pièces de pompes pour éviter la contamination avec les autres métaux », précise M. Allard.
La constance quant à l’importance du tri des matériaux a été déterminante pour consolider le projet. « Il a fallu sensibiliser les équipes car chacun devait mettre l’épaule à la roue afin que les matières se retrouvent au bon endroit. Nous avons fait en sorte que chacun comprenne la raison d’être de cette initiative qui nous permet en bout de ligne d’avoir des pièces de qualité. Nous avons même organisé une visite avec les mécaniciens chez le fournisseur afin qu’ils puissent voir concrètement comment sont fabriquées les pièces à partir du métal que nous avons récupéré », ajoute Gérald Saulnier, superviseur d’entretien.
Il est notable que les équipes sont engagées à cultiver les bonnes pratiques et à recycler adéquatement les matériaux. « C’est un changement qui s’est fait naturellement avec les générations. Le contenu des bacs est conforme et les employés sont soucieux de mettre les bonnes matières aux bons endroits. Il faut poursuivre nos efforts. La conscience environnementale est beaucoup plus présente », conclut-il.