Un prototype prometteur pour l’usine de Laterrière
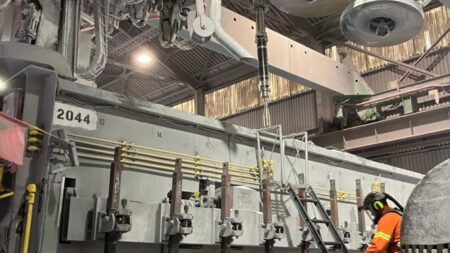
Le projet de développement du prototype de contact pointerole à l’Usine Laterrière représente une avancée significative dans l’amélioration des performances des cuves d’électrolyse. Menée par une équipe multidisciplinaire composée des deux groupes d’électrolyse et du groupe instrumentation du CRDA ainsi que les équipes de maintenance, opération et technique de l’usine Laterrière, cette initiative incarne un modèle de collaboration. Elle témoigne des efforts communs pour contribuer à l’amélioration continue des opérations, dans un objectif de réduction des émissions de gaz à effet de serre (GES) et d’optimisation des processus industriels.
Ce prototype de casseur-alimenteur est destiné à être installé dans les cuves d’électrolyse de la technologie P155. En plus de son rôle de base visant à casser la croûte tout en injectant simultanément l’alumine dans le bain, cette innovation vise à aider le contrôle de procédé, ce qui permettra de réduire les effets d’anodes indésirables et, par conséquent, les émissions de GES.
Selon Bastien Pansiot, scientifique en charge de l’amélioration des procédés, l’instrumentation est essentielle pour une détection précoce des anomalies : « Sans cet outil et les données qu’il fournit, nous sommes aveugles quant à la bonne distribution de l’alumine là où elle est nécessaire. Grâce à ces nouveaux outils de contrôle, nous pouvons détecter précocement des anomalies, ce qui rend les interventions plus rapides et efficaces, et permet ainsi de se prévenir de certains effets d’anodes. »
Garantir la robustesse du prototype
Avant son implantation, le prototype a été testé pendant six mois en laboratoire et en milieu contrôlé. Ces tests ont permis de qualifier l’usure des matériaux et d’évaluer la réaction du mécanisme dans des conditions plus difficiles. Forts des enseignements tirés de ces essais, des ajustements ont été apportés pour rendre le prototype plus robuste et performant encore. Depuis plus d’un mois, le deuxième modèle est en phase de test sur une cuve, avec des améliorations visant à augmenter l’efficacité du dispositif. Jonathan Gilbert, chargé de projet en R&D, souligne l’importance de cette démarche qui se veut évolutive: « Nous sommes en mode itératif, c’est-à-dire que nous tirons des enseignements sur chaque phase du projet. Cela nous permet d’apprendre et d’ajuster les caractéristiques du prototype en continu en fonction des performances observées. »
Le projet est divisé en plusieurs phases. Toute d’abord, les étapes de conception et de prototypage, qui ont été faites en début d’année. À la suite des deux premières étapes, la phase suivante consistait à tester les prototypes dans une cuve. Ce test ayant été couronné de succès, l’étape suivante consistera à augmenter progressivement le nombre de cuves testées, réduisant ainsi les risques à chaque étape du processus. L’objectif final est de déployer la technologie à l’Usine Laterrière et ultimement la transférer à l’usine Grande-Baie, en garantissant la fiabilité du système tout en optimisant progressivement son efficacité.
Une collaboration essentielle
Le succès du projet repose en grande partie sur la collaboration étroite entre tous les intervenants. Dès les premières étapes, les électrotechniciens et les mécaniciens ont été impliqués dans le processus. Jean-François Plourde, support opérationnel et opérateur, partage l’importance de cette collaboration : « Nous avons mis à contribution l’expérience de nos employés, puisque ce sont eux qui connaissent le mieux les opérations. Nous avons pu identifier les irritants et apporter des solutions pratiques. »
« Cette étroite collaboration a également permis aux employés de s’approprier le projet et de faire partie prenante de la solution. Leur participation a été l’une des clés de compréhension pour l’implantation de la technologie », ajoute Patrice Perron, scientifique en R&D au CRDA.
L’innovation technologique ouvre la voie à de nouvelles perspectives pour un avenir plus durable grâce à l’instrumentation, nous permettant ainsi de mieux mesurer et contrôler des paramètres cruciaux, et ainsi d’améliorer les processus en continu.
Jonathan Gilbert conclut sur une note positive : « On ne peut pas améliorer ce qu’on ne peut pas mesurer ! L’instrumentation nous ouvre des portes et nous permet d’avoir de nouveaux angles de vue. Plusieurs améliorations vont pouvoir naître de cela. Pour l’instant, le fondement du travail est bien fait et nous avons une bonne assise, reste à monter en régime et à continuer le travail exemplaire de tous. »