Les pots d’étanchéité inclinés implantés à l’Usine Grande-Baie
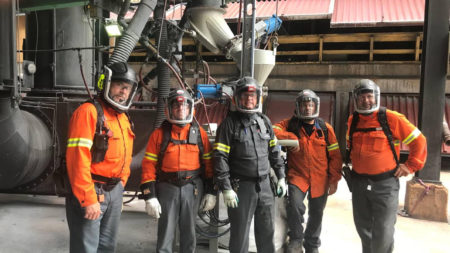
Sur la photo, de gauche à droite : Gervais Latullipe, Marc Dufour, Michel Côté, Michel Gravel et Laurent Grenier. Absents : Carol Imbeault, Raymond Emond, Matthieu Tremblay et Frédéric Tremblay.
Programmés et installés depuis juillet 2021, les pots d’étanchéité inclinés ont atteint les résultats espérés au centre de traitement des gaz de l’Usine Grande-Baie. Alors que les employés ne sont plus obligés de nettoyer quotidiennement et manuellement chacun des 66 collecteurs, différents risques de santé et de sécurité au travail sont désormais évités. La stabilité et la performance des opérations ont également été améliorées.
Interrogé quant aux raisons de la concrétisation du projet des pots d’étanchéité inclinés à l’Usine Grande-Baie, Michel Côté, technicien de procédé, Épuration et environnement, a répondu qu’une solution devait absolument être mise en place pour diminuer l’exposition des travailleurs aux contaminants et automatiser la manœuvre.
Avant, la position horizontale des toiles canevas de nos pots d’étanchéité faisait en sorte qu’ils étaient plus sensibles aux blocages. L’élément qui est à la source de ces blocages s’appelle de la calamine, ou de la scale en anglais. Cette calamine est notre plus grand ennemi, car elle élimine la fluidisation de ces équipements. En n’ayant aucun procédé automatique pour y remédier, les employés devaient nettoyer quotidiennement et manuellement les collecteurs, s’exposant ainsi à différents contaminants », explique-t-il.
En développant des pots d’étanchéité inclinés adaptés à leurs besoins, l’air peut continuer de passer malgré la calamine qui s’accumuler, car la partie du haut continue de permettre la fluidisation. L’équipement peut ainsi poursuivre son rôle, soit celui de transporter le matériel dans le procédé. L’automatisation favorise donc la stabilité opérationnelle en plus d’éviter d’exposer les employés à des poussières qui ont été en contact avec les gaz bruts des cuves.
« Le développement du projet s’est fait en équipe. Un prototype a été testé pendant un an afin de valider son bon fonctionnement. Grâce à l’équipe d’ingénierie menée par Laurent Grenier et les entreprises Technosoude, Moreau, Électricité Grimard, Shipshaw Électrique, Norda Stelo, Engrenage Provincial et le groupe des Technologies de l’information (TI) de Rio Tinto, les travaux ont été réalisé en dix mois seulement. Un montant de 3,5 millions a été octroyé par le comité d’investissement de l’usine. Le projet a finalement été complété et nos objectifs ont pu se réaliser », souligne M. Côté.