Les équipes se mobilisent à l’Usine Laterrière
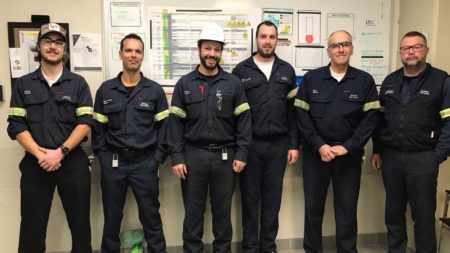
L'équipe ayant contribué au succès de l'opération:
Voici le nom des gens sur la photo de gauche à droite : Dannick Gauthier, Jean-François Martel, Simon Lessard, Simon paré Desjardins, Jules Simard et Frédéric Tremblay.
D’importants travaux ont eu lieu en avril et en mai au secteur Haute Tension de Laterrière. Différents corps de métiers indépendants ont été interpellés pour prêter main-forte à l’équipe de l’usine qui traversait une période éprouvante, en raison de l’augmentation des pannes qui précarisaient la production d’aluminium. Dans une véritable course contre la montre, les travailleurs d’Énergie Électrique, de Gestion des actifs, d’Hitachi et de l’Usine Laterrière ont uni leur savoir-faire pour un retour à normale dans les meilleurs délais.
Deux scénarios sont survenus en même temps et imbriqués l’un dans l’autre. Dans un premier temps, au début du mois d’avril, on a constaté que les redresseurs à la Haute tension avaient un problème de surchauffe. Il était impératif de s’assurer que ceux-ci soient bien refroidis avant l’arrivée des chaleurs de l’été. Autrement, l’intensité des salles de cuves devrait être réduite pour éviter que les équipements ne deviennent trop chauds.
La problématique était connue, mais était devenue plus préoccupante considérant l’augmentation des pannes observées sur ces équipements. « L’Usine Laterrière subissait des baisses de production chaque jour en raison des pannes. C’était trop risqué de continuer d’opérer avec ce niveau de courant, il fallait baisser l’intensité. Qui dit diminution de l’intensité, dit baisser la production d’aluminium », fait valoir Hugo Simard, ingénieur électrique, Gestion des actifs Opérations Québec.
« On a fait une cellule de crise avec différents intervenants d’Énergie Électrique, de Gestion des actifs, de l’ingénierie et de l’usine pour trouver des solutions pour refroidir les redresseurs. Pour être certain d’avoir le temps de mener à terme le projet de réfection complète, il fallait stabiliser les redresseurs pour la durée des travaux », explique Guillaume Villeneuve, ingénieur Fiabiliste, Gestion des actifs Opérations Québec.
En un temps record, huit imposants climatiseurs ont été installés sur les redresseurs dans la haute tension, à travers les opérations de l’usine qui est demeurée en fonction. À l’intérieur d’au plus cinq semaines, les appareils étaient arrivés sur le site, installés et opérationnels.
C’est exceptionnel et c’est une belle fierté en terme d’efficience et d’efficacité d’exécution. Au départ, on ne savait pas quoi envisager. Nous avons trouvé une vingtaine de solutions que l’on a travaillées de façon indépendante pour voir laquelle était réalisable avant l’été », poursuit M. Villeneuve.
« L’usine était à grand risque de panne, ce qui nous menaçait de perdre une salle de cuves. Pour une usine d’aluminium, perdre une salle de cuve, c’est un des pires scénarios. C’est ce qui fait en sorte que toutes les équipes ont travaillé sans relâche pour éviter ce bris. Tout le monde s’est mobilisé pour venir aider l’Usine Laterrière », précise Hugo Simard.
La veille de la mise en marche des climatiseurs, un second bris est survenu, mais cette fois sur le transformateur qui alimente les redresseurs en électricité. Un défaut électrique interne le rendait impossible à redémarrer. Le projet s’est donc retrouvé en pause.
La première étape consistait à faire le diagnostic spécialisé pour trouver de quelle nature était le bris du transformateur. De façon coordonnée, les experts d’Énergie Électrique et d’Hitachi ont travaillé en équipe pour faire les tests et se partager les résultats. Une collaboration qui a démontré un grand professionnalisme. Ne sachant trop quelle avenue envisager pour la reprise des activités, l’Usine Laterrière était sur le qui-vive.
«L’enjeu était de savoir si le bris était réparable sur place. Dans les trois premiers jours, on ne savait pas si on allait devoir sortir le transformateur à l’extérieur, puis l’envoyer par train ou par véhicule à Sherbrooke, ou encore construire un atelier sur le site avec un hangar pressurisé. Ce genre de manipulation est aussi précaire qu’une opération à cœur ouvert. C’était très stressant pour les opérationnels en usine. Sortir le transformateur pour le réparer aurait nécessité des délais de 3 à 4 mois », mentionne Guillaume Villeneuve.
Heureux dénouement, le transformateur a finalement pu être réparé sur place en 12 jours, ce qui représente un véritable tour de force pour une opération du genre qui, d’ordinaire, s’effectue en 35 jours.
« Les exploitants ont dû être très présents! Ces travaux ont eu un lourd impact pour eux puisque pour faire entrer ces chantiers, nous avons dû travailler très tôt le matin, en soirée et en fin de semaine », souligne Hugo Simard.
C’était impressionnant de voir le niveau d’expertise qu’on avait sur le site. Que ce soit les experts de réparation de transformateurs d’Hitachi et d’Énergie électrique, l’équipe usine qui encadrait les opérations pour s’assurer que tout était fluide, ou l’équipe de la gestion des actifs qui s’assurait qu’on n’oublie aucun morceau et préparait les coups d’avance, tout le monde travaillait comme une seule et même grande équipe parce que le temps était compté », conclut Guillaume Villeneuve.