Réparation majeure d’un équipement essentiel à la continuité des opérations
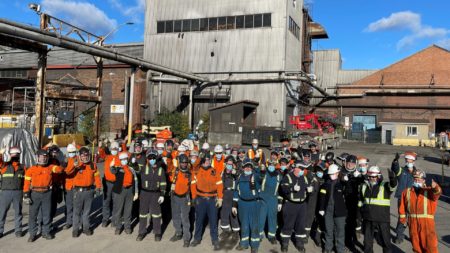
L'équipe ayant participé au projet de réparation de la presse des anodes.
En janvier dernier, l’équipe d’Arvida-AP60 a dû se retrousser les manches rapidement pour trouver une solution viable afin de réparer une fissure majeure décelée sur le cylindre principal de la presse des anodes. Ingéniosité, rapidité et travail d’équipe, voici ce qui aura permis à l’équipe de mener à bien ce projet d’envergure, et ce, en toute sécurité.
Aussitôt la fissure détectée, l’usine a mis en place une cellule de crise et a déployé un groupe de travail multidisciplinaire pour identifier des solutions potentielles. La presse des anodes est l’unique équipement de formage permettant d’approvisionner l’usine en anodes vertes. Donc, plusieurs actions à court terme ont dû être réalisées afin de sécuriser l’opération de l’équipement.
Nous nous sommes retrouvés devant une page blanche, puisque dans toute l’histoire de la presse des anodes, c’était la première fois que l’équipe devait faire face à un tel bris sur l’équipement. Afin de rendre le projet viable et d’éviter d’entraver notre production, nous avons étudié plusieurs scénarios, comme la réparation par soudage, le remplacement des composantes fissurées, l’achat d’une presse neuve, le changement technologique, etc. », explique Michaël Manning, ingénieur électrique, centre de production d’anodes d’Arvida.
Après un travail de recherche rigoureux, l’équipe a finalement réussi à mettre la main sur les dessins de fabrication de la presse, qui se trouvaient alors en Ohio, aux États-Unis. En rachetant la propriété intellectuelle des dessins, l’équipe a été en mesure de mettre en place toutes les étapes nécessaires à la réparation de l’équipement.
« L’idée était de remplacer les pièces fissurées tout en conservant les composantes d’origine de la presse. Les internes du cylindre ont été conservées et récupérées, mais nous avons fait des recherches dans les marchés émergents pour trouver un fabricant pouvant nous produire les pièces sur mesure. La pièce maîtresse a finalement été conçue en Italie, il fallait donc prévoir des délais de production et de transport. Pendant ce temps, nous nous sommes penchés sur l’ingénierie et la méthode de remplacement », témoigne David Boudreault, chargé de projet sénior.
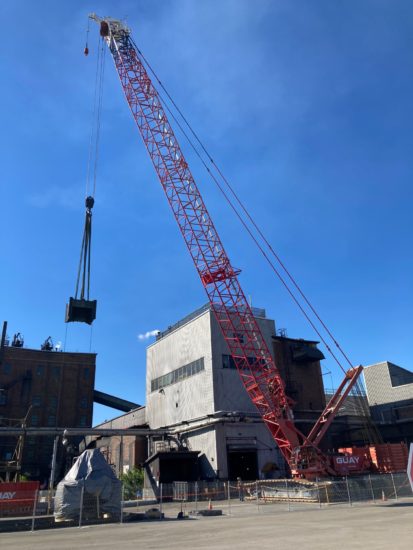
Levage critique d’une des composantes principales de la presse HPM.
Un travail de collaboration
Pour éviter d’impacter la production durant cet arrêt majeur de huit semaines, l’équipe devait se bâtir un inventaire d’anodes significatif. Un inventaire stratégique de l’ordre de 48 000 anodes a donc été réalisé en amont. L’Usine Grand-Baie a également prêté main-forte en proposant une fenêtre opérationnelle permettant de produire 21 000 anodes du même format.
En travaux préparatoires, l’équipe a également décalotté le toit du bâtiment existant pour le remplacer par un toit amovible et ainsi sortir les pièces et procéder au démantèlement de la presse. Elle a aussi dû trouver un espace pour aménager un atelier mécanique afin de manutentionner les pièces et d’effectuer le travail de minutie des internes. C’est finalement un bâtiment à même les installations d’Arvida qui a été ciblé.
« Nous avons trouvé l’atelier 8 qui se trouve à être l’atelier de réfection des transformateurs d’Énergie Électrique. Le bâtiment possédait l’espace requis ainsi qu’un pont roulant de 75 tonnes qui avait la capacité exigée pour effectuer les travaux », ajoute M. Boudreault.
Malgré la complexité technique du projet ainsi que les différents enjeux entourant la logistique, les travaux ont été effectués en toute sécurité. « Nous parlons d’un projet qui, normalement, se serait échelonné sur deux ans. Nous aurons réussi à le compléter en environ 11 mois. Tous les intervenants étaient impliqués, autant les entrepreneurs que les gens d’entretien et l’équipe dédiée. Nous sommes convaincus que la participation de tout le monde est la clé du succès de ce projet durant lequel aucun événement SSE n’est survenu », termine Pascal Therrien, chef de service du secteur.
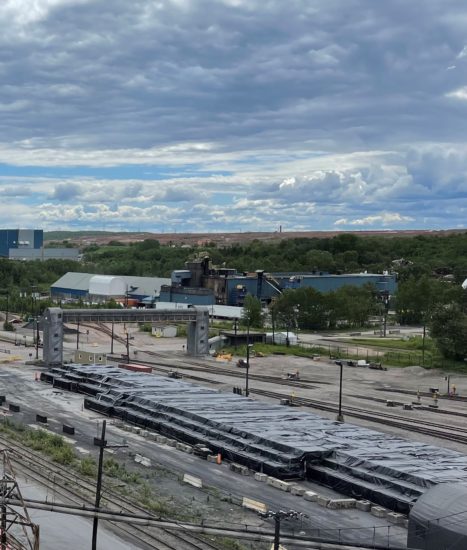
Une partie de l’entreposage des anodes d’Arvida (20 388 anodes vertes).
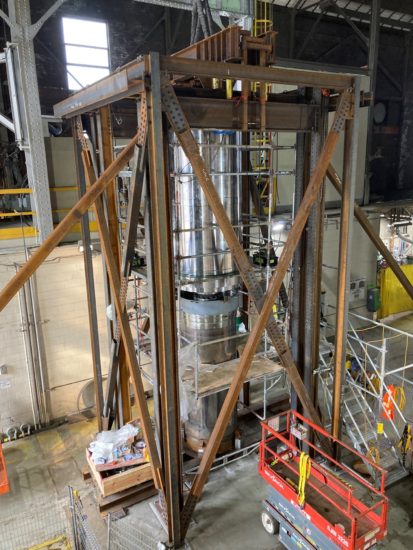
Assemblage du nouveau cylindre avec son piston au bâtiment 8.