Une solution novatrice pour l’entretien des silos d’alumine de l’Usine Alma
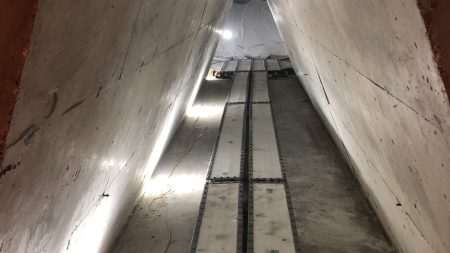
Les trois silos contenant chacun 5 500 T d’alumine servant à l’approvisionnement les salles de cuve de l’Usine Alma ont récemment connu d’importants travaux. Ce projet complexe visant le remplacement des toiles de soutirage des convoyeurs fluidisant s’est échelonné sur une période de six mois. Une équipe multidisciplinaire dédiée et la confiance de la direction ont contribué au succès de la démarche.
L’automne dernier, une activité de Kaisen a réuni des employé(e)s de plusieurs secteurs (ingénierie, procédé, entrepreneurs, opérations, gestion des actifs) pour trouver une solution innovante de remplacer les toiles de soutirage. L’abrasion créée par l’alumine a pour effet d’user la toile qui est faite d’un textile. Avec le temps, celle-ci peut se fissurer et entraîner des blocages qui empêchent d’en extraire l’alumine. Les toiles n’ayant pas été changées depuis l’installation des silos à l’ouverture de l’usine, il y a près de 25 ans, la possibilité d’un bris imminent représentait un risque.
En parallèle, un projet d’ingénierie laissait présager les travaux qui atteindraient 27 M$ US. L’ingéniosité de l’équipe multidisciplinaire a plutôt permis de réaliser les travaux au coût d’un à 1,5 M$ par silo.
« Nous avons réuni plusieurs personnes autour de la table pour trouver des solutions originales pour aller enlever l’alumine qui pouvait être résiduelle dans le silo. Nous pensions qu’il pouvait y avoir des morceaux d’alumine agglomérée qui pouvaient tomber et boucher le silo, ce qui occasionnerait d’importants délais », exprime Simon Pilote, chef de service, Opérations et SOP.
« Nous avons pris des images 3D dans les silos et nous avons fait des trous sur le côté pour voir l’état de l’alumine. Nous avons décidé d’abaisser le niveau le plus possible et de siphonner ce qui restait de manière à se faire un chemin qui nous permettrait d’aller remplacer les toiles de soutirage, » poursuit-il.
Les travaux, qui se sont échelonnés sur une période de six mois, ont nécessité une imposante logistique. «Les CTG et les salles de cuves nécessitent une alimentation en alumine de 35 T à l’heure, il fallait trouver une façon de continuer de les approvisionner pendant les travaux », fait valoir l’ingénieur Jean-Philippe Côté, Leader Sectoriel – Ingénierie, Electrolyse, SOP.
L’approvisionnement en alumine a donc été effectué par camion, à raison d’un changement de véhicule toutes les heures. . Par moment, jusqu’à 57 personnes travaillaient sur le chantier sur une période de 24 heures. Malgré les risques potentiels, aucun incident SSE ne s’est produit.
« Notre client, soit le secteur de l’électrolyse n’a eu aucun impact », soulignent les deux collègues. « Outre la réussite sur le plan de la sécurité, de l’échéancier et des coûts, la façon dont toute l’équipe s’est comportée durant la période des travaux a été fantastique. Malgré les embûches, les craintes et les risques inhérents au projet, toute l’équipe est restée de bonne humeur, impliquée et dans un état d’esprit de collaboration qui a permis l’atteinte d’un objectif commun », ajoute M. Côté.
En tout, 400 T d’alumine ont été siphonnées puis récupérées dans le procédé. Les améliorations apportées aux silos et procédures demeurent en place et permettront de planifier des arrêts d’entretien à intervalles de trois à cinq ans.