Un arrêt majeur de 31 jours réalisé de main de maître
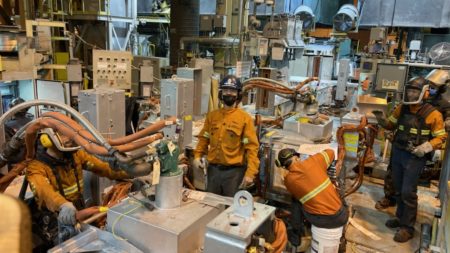
L'arrêt majeur s'est déroulé sans anicroche grâce à une coordination exemplaire et un bon travail d'équipe.
Du 20 février au 22 mars dernier, les équipes du Centre de coulée de l’Usine Alma ont effectué le plus gros arrêt jamais réalisé en région sur des fours réfractaires. Un projet totalisant 12 550 heures de travail consécutives, réparties sur 31 jours. En plus de procéder à la réfection totale des fours, huit autres projets se sont greffés à celui-ci, dont l’installation d’unités de filtration permettant d’augmenter la propreté du métal pour répondre aux exigences du marché. En 2022, ce sont 6.7 millions de dollars qui ont été injectés dans ce projet d’envergure. La planification de chaque heure travaillée, l’engagement et la disponibilité des employés sont les ingrédients gagnants qui ont permis aux équipes de réaliser ce projet d’exception, et ce, à travers la bonne humeur et le positivisme.
Arrivés en fin de vie, les fours quatre et cinq pour la machine de coulée horizontale 1 (MCH1) au Centre de coulée, devaient être reconstruits à neuf, nécessitant ainsi un arrêt majeur. « Le but de l’arrêt était d’être le plus rapide possible en effectuant un travail de qualité, et ce, en misant sur la sécurité des gens. Le secret d’un arrêt majeur repose sur plusieurs facteurs importants, la collaboration des parties prenantes, la préparation et les rencontres quotidiennes sont des éléments clés », explique Steeve Perron, coordonnateur des arrêts majeurs.
Depuis 20 ans, je vis à travers les arrêts majeurs et c’est l’une des rares fois où j’ai vu des gens nettement moins épuisés après une telle séquence de travail. Je veux souligner le succès et le rendu des travaux qui sont attribuables, entre autres, à la coordination exemplaire des équipes et à l’attitude positive de tous. Même dans les périodes plus difficiles, le ton n’a jamais monté et tout le monde était en mode solution », témoigne Richard Gauthier, surveillant principal, Centre de coulée.
Le défi supplémentaire du projet était également d’intégrer et d’installer un nouvel équipement de production à travers la poursuite des opérations du Centre de coulée. « On se faisait des passes pour coordonner nos travaux et arriver à libérer des plages horaires pour que tout le monde puisse effectuer leur travail, c’était en quelque sorte une danse chorégraphiée. Au final, il n’y a pas de hasard au succès du projet, car nous étions en mode préparation depuis des mois », ajoute Jean-Michel Gagnon, ingénieur entretien.
« Nous avons réussi à établir une bonne routine de communication en effectuant deux rencontres par jour durant l’arrêt. Cela nous permettait de mettre les bons joueurs autour de la table pour planifier ce qui s’en venait et adresser les problèmes en temps réel », mentionne Mathieu Sauvageau, leader sectoriel, Centre de coulée.
En parallèle au projet principal, les équipes ont travaillé à l’installation et la mise en service de deux équipements de filtration en plus des équipements connexes. « L’objectif du projet CFF (ceramic foam filter), était dans un premier temps d’améliorer la propreté du métal et aussi d’automatiser la ligne de filtration pour empêcher les incidents SSE dans le futur. Avec l’installation d’une dérivation sur la ligne de coulée, le métal se fait filtrer pour sortir avec un niveau de propreté plus élevé. Ce projet était d’un haut niveau de complexité, car il exigeait de nombreux changements techniques, dont l’ajout de lignes de gaz, de capteurs et d’instrumentation. Le tout, pour capter de nouveaux marchés potentiels et répondre à une demande client qui souhaitait avoir du métal filtré de haute qualité », d’expliquer à son tour Jean-Philippe Côté, chargé de projet, Centre de coulée.
Au terme des travaux, aucun incident SSE n’est survenu. Ce que les employés retiennent après un projet d’une telle étendue, c’est la rigueur et la bonne humeur qui a régné sur le chantier pendant les 31 jours travaillés.
Le projet en chiffre :
- 31 jours
- 12 550 heures de travail consécutives
- 7 millions d’investissements
- 0 incident SSE