Importants travaux au centre de calcination : les employés font preuve d’ingéniosité
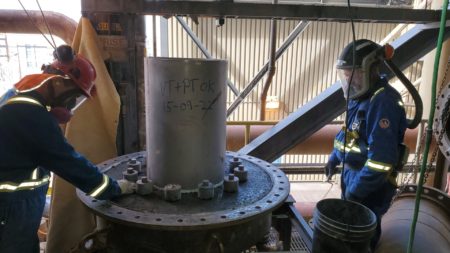
La conception de la tuyère du pré-refroidisseur a été revue, la faisant passer de 2 morceaux à un seul.
D’importants travaux d’entretien ont eu lieu lors de l’arrêt de l’unité #1 du centre de calcination, en septembre dernier. Mobilisant une centaine de personnes et s’échelonnant sur 450 heures, celui-ci devait permettre de remplacer le lit fluidisé du réservoir de rétention, une conduite de transfert d’alumine et la tuyère du pré-refroidisseur.
Le lit de fluidisation du réservoir de rétention étant obsolète et commençait à avoir des problèmes d’approvisionnement. Les regards se sont donc tournés vers une technologie d’une usine jumelle en Europe. Celle-ci datait toutefois d’une quinzaine d’année et son coût de l’ordre d’un million de dollar était un frein au projet.
Grâce à sa capacité à innover, l’équipe de l’arrêt a plutôt opté pour un concept hybride du lit de fluidisation.
Le concept est beaucoup plus simple et l’efficacité est là. En y réfléchissant, nous en sommes venus à la conclusion que nous pouvions faire différemment avec d’autres matériaux, tout en étant aussi résistants, en nous inspirant de ce concept externe et en conservant certains de nos paramètres. Nous avons adapté ce qui se faisait ailleurs pour beaucoup moins cher », fait valoir Dany Bonneau, ingénieur d’entretien.
« Nous avons mis des tuyères comme l’usine jumelle, mais en SS310 et en les recouvrant de billes d’alumine comme notre ancien lit. Nous avons enlevé des supports qui n’étaient finalement pas nécessaires, revu le concept des soudures et de la préfabrication. Nous avons ainsi pu réduire le temps d’installation au chantier et les coûts pour un réel de 220k$», précise Éric Tremblay, technicien entretien mécanique au centre de calcination.
Pour ce qui est de la conduite d’alumine, elle devait initialement, être complètement remplacée par une structure neuve. Pour ce faire, il était nécessaire d’avoir recours à une grue 600 T.
« La conduite d’alumine, c’est un grand tuyau qui fait quatre étages de haut. Le sortir de l’usine engendrait des coûts de près d’un demi-million de dollars. Après analyse, il a été convenu de remplacer son réfractaire interne seulement, avec des sections superposées, ce qui a considérablement réduit les coûts », fait valoir M. Bonneau.
« Nous avons enlevé des sections de plancher pour utiliser notre pont roulant existant. Nous avons récupéré la conduite d’acier existante et remplacé uniquement le réfractaire interne par des manchons préfabriqués soutenus par des supports muraux. Un isolant de fibre céramique a été injecté entre la paroi et les manchons pour les maintenir en place. Le projet a ainsi été abaissé à 175k$ l’unité », mentionne M. Tremblay.
Quant à la tuyère du pré-refroidisseur elle avait été la cause une perte de 3102 T de production en 2021. En mode élimination des défauts, sa conception originale en deux sections a été revue, la faisant passer de deux morceaux à un seul, ce qui élimine ainsi le risque de séparation par usure.
Une centaine de travailleurs ont pris part aux travaux. Nous sommes parvenus à avoir les mêmes entrepreneurs que dans les trois dernières années, ce qui a permis une stabilité sur les chantiers et un gain sur la vitesse d’exécution. Grâce au travail d’équipe nous avons pu livrer un chantier dans les délais en réalisant d’importantes économies, » conclut Jean-Philippe Minier, planificateur arrêt majeur.
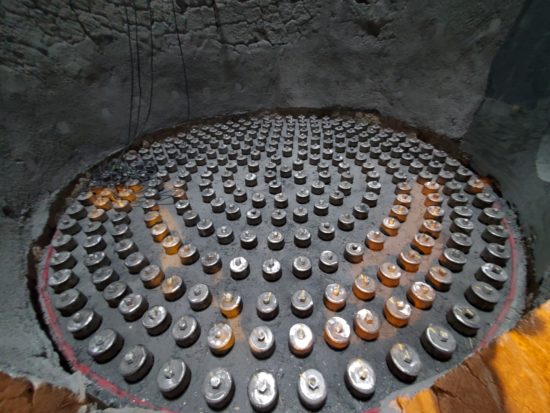
L’équipe de l’arrêt s’est inspirée de ce qui s’est fait dans une usine jumelle d’Europe, pour penser un concept hybride du lit de fluidisation.