Tour de maître pour le démarrage de la 2e chaîne de précipitation en continu
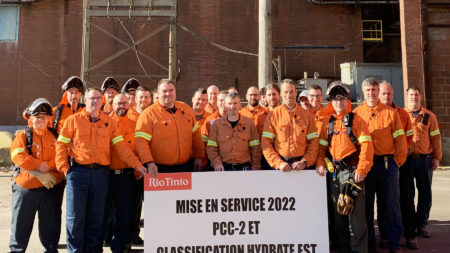
Le démarrage de la deuxième chaîne de précipitation en continu et classification optimisée a eu lieu au printemps dernier. Véritable tour de maître, ce projet de l’ordre de 23 M$ a pris forme sans interrompre les opérations courantes de l’usine Vaudreuil. Pendant les neuf mois qu’a duré la phase de construction, une centaine d’employé(e)s ont profité des arrêts planifiés pour effectuer les modifications aux installations existantes, soit 13 réservoirs à Hydrate Est. Un exploit remarquable en matière de coordination et de collaboration!
« C’est un gros défi! Nous travaillons dans des endroits restreints qui présentent des contraintes thermiques. C’est un environnement de travail complexe. Pour 110 000 heures d’exposition, on ne dénombre aucune blessures consignables », explique Pascal Bejjani, ingénieur, chef de projet, services Ingénierie, Usine Vaudreuil.
L’efficacité avec laquelle le démarrage de la deuxième chaîne de précipitation en continu a eu lieu a suscité l’étonnement de plusieurs. Un succès attribuable à l’excellente collaboration des gens d’opération et d’entretien qui ont été nombreux à participer à toutes les phases du projet, de la conception, à la construction, jusqu’à la phase de vérification pré-opérationnelle (VPO) et de démarrage, ce qui a permis de corriger les problématiques dès qu’elles se présentaient.
Sécurité des procédés et augmentation de la capacité de production
Les travaux de modification touchent environ 18 % des réservoirs à Hydrate Est et permettent de procéder à une précipitation en continu plutôt qu’à une précipitation en mode fournée (batch).
L’augmentation de la capacité de production d’alumine est certes un élément positif, mais c’est d’abord pour assurer la sécurité des procédés que ces améliorations ont été apportées.
Un procédé batch, ou fournée, demande des opérations quotidiennes sur chacun des réservoirs. Ces manipulations représentent un risque en soi et font en sorte qu’il peut y avoir un débordement de réservoir. La chaîne en continu minimise les activités quotidiennes de manipulation et diminue très fortement les risques qui y sont associés. Au-delà de la santé et la sécurité, ces modifications permettent un gain de production qui n’est pas négligeable par l’élimination des temps de remplissage, de vidange et la diminution de la fréquence de nettoyage », explique Claude Lalancette, représentant du promoteur, projets stratégiques, Usine Vaudreuil, Aluminium.
Classification optimisée
Le circuit de classification de l’usine a également été optimisé afin d’augmenter la génération de grosse amorce requise pour alimenter le circuit de la nouvelle chaîne de précipitation (améliorer la productivité) et engendrer de la liqueur usée (augmentation de débit).
L’un des éléments particuliers du projet en termes de recherche et développement technologique est la réalisation du cône Alain Guilbert, qui porte le nom de son idéateur qui œuvre au sein de l’usine Vaudreuil depuis 30 ans. Proposée au début des années 2000, cette solution s’inscrit au niveau des procédés de l’usine afin d’améliorer le contrôle de l’écoulement dans le réservoir d’amorce et d’obtenir le plein potentiel de la précipitation en continu à Hydrate Est. « Nous avons étudié cette idée, nous en avons fait l’ingénierie et l’avons construit», précise M. Bejjani.
Le cône Alain Guilbert constitue un élément de la classification. C’est à l’intérieur de celui-ci qu’est entreposée la grosse amorce, l’objectif étant d’éviter l’accumulation d’hydrate qui entraîne des opérations de nettoyage à intervalle de quatre à six mois. « Le cône permet de diminuer la fréquence de nettoyage des réservoirs. Nous sommes à la phase d’essai. Nous avons fait des ajustements au système et jusqu’ici, tout fonctionne bien. […] Nous visons moins d’un nettoyage par année », poursuit M. Lalancette.
Équipe intégrée
La phase d’étude et la phase d’exécution ont été réalisées selon un organigramme d’équipe intégrée traditionnel. L’expertise des représentants de différents secteurs a été mise à profit. « La réalisation du projet dans un mode conception-construction dans l’usine en production a nécessité l’intégration du technicien mécanique Représentant Utilisateur (Stéphane Gauthier) et de l’opérateur Représentant Énergie-Zéro (Rémi Villeneuve) dans toutes les étapes de conception. Cela a permis le transfert efficace de connaissance », mentionne Pascal Bejjani.
Une première chaîne de précipitation en continu a été mise en service en 2019. Le modèle de la seconde chaîne est néanmoins un concept appelé à être répliqué afin que l’usine fonctionne à 100 % de précipitation continue. « Les ressources clés qui ont participé à la première phase ont pu transmettre leur expertise afin d’améliorer la conception. Nous avons bâti sur le savoir et les connaissances déjà acquises », poursuit-il.
Tous les opérateurs ont reçu une formation avant la phase de vérification pré-opérationnelle, des connaissances qu’ils ont pu mettre en pratique sur le terrain au moment de démarrer les équipements.
La contribution des membres de l’équipe d’opération a été un facteur clé de réussite du démarrage de la classification optimisée ainsi que de la chaine de précipitation continue deux. C’est un bel exemple d’engagement de l’équipe de l’usine Est dont nous pouvons tous être fiers », note Sébastien Delisle Chef de service usine Est et BHB.
Le démarrage hautement réussi de la deuxième chaîne de précipitation en continu et classification optimisée est le résultat du savoir-faire des équipes qui ont su se mobiliser pour contribuer au succès de ce projet novateur qui s’inscrit dans la pérennité de l’usine Vaudreuil.
En bref :
- 23 M $ en investissement
- 900 mètres de tuyauterie
- Pic de 100 employés l’automne dernier
- Environ 18 % des réservoirs des hydrates ont été touchés par les travaux
- Installation d’une nouvelle salle électrique pour augmenter la capacité du secteur
- 110 000 heures d’exposition : aucune blessures consignables