Plateforme d’industrialisation : du laboratoire à l’usine
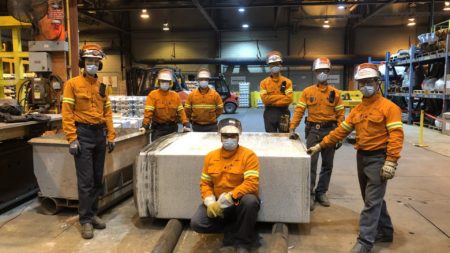
L'équipe ayant travaillé à la création de la plateforme d’industrialisation.
Et s’il était possible de faire l’essai de différents procédés de coulée avant même de les implanter en usine ? Voici la question qui a mené à la création de la plateforme d’industrialisation, active depuis le 18 octobre 2021. Cette plateforme permet de poursuivre le développement pour l’amélioration du procédé, et ce, avant d’exporter des solutions matures en usines.
La création de cette entité unique, composée de plusieurs acteurs importants dont le Centre de recherche et développement d’Arvida (CRDA), l’équipe de l’Usine Dubuc, celle de Grande-Baie et Laterrière (P155) ainsi que l’équipe de l’Ingénierie, est une première dans l’histoire de Rio Tinto.
Laboratoire à grande échelle
Le CRDA développe, en continu, plusieurs projets visant l’amélioration des procédés dans les diverses installations de Rio Tinto. Une multitude de tests sont alors réalisés en laboratoire, à petite échelle, avec une unité de coulée.
La création de la plateforme d’industrialisation permet désormais d’exporter ces solutions et de les éprouver à l’Usine Dubuc. Cette transition entre le CRDA et l’usine nous assure une plus grande latitude, car il y a moins de crainte de perte et d’impact sur la production. Il s’agit d’une grande valeur ajoutée pour l’organisation puisque nous pouvons jouer avec les extrêmes, cela donne de la vitesse et plus de performance à nos projets », explique Josée Colbert, scientifique de recherche au CRDA.
Pour être en mesure de reproduire la technologie du CRDA en format semi-industriel, l’équipe de Dubuc s’est retroussé les manches afin de remettre en fonction un four de coulée qui était arrêté depuis plusieurs années. « Nous avons travaillé à actualiser l’équipement pour le remettre en fonction et accueillir les nouveaux procédés. Les employés se sont appropriés le projet et ont travaillé très fort. Il faut d’ailleurs souligner leur engagement parce qu’ils ont mené le projet d’une main de maître et ont contribué à son succès », témoigne Louis Tremblay, superviseur à l’opération.
Ultimement, le procédé sera intégré à P155 dans sa forme industrielle. Il s’agit également d’une porte d’entrée pour l’essai de nouveaux produits qui pourraient éventuellement découler de demandes de clients. « Nous pourrons désormais développer la recette de différents alliages à l’extérieur des usines pour ensuite fournir le mode opératoire. Cela nous évitera les ajustements nécessaires en usine et les risques de perte de production reliés au développement d’un nouvel alliage », ajoute Luc Tremblay, chef de projet.
Grâce à la plateforme d’industrialisation, nous avons aussi une meilleure connaissance de ce qui pourrait se produire en usine, ce qui améliore l’aspect santé-sécurité, souligne Julie Dussault, surveillante principale. Beaucoup de sphères de l’organisation sont impliquées dans ce maillage qui nous permet de travailler main dans la main pour améliorer de façon globale nos pratiques ».